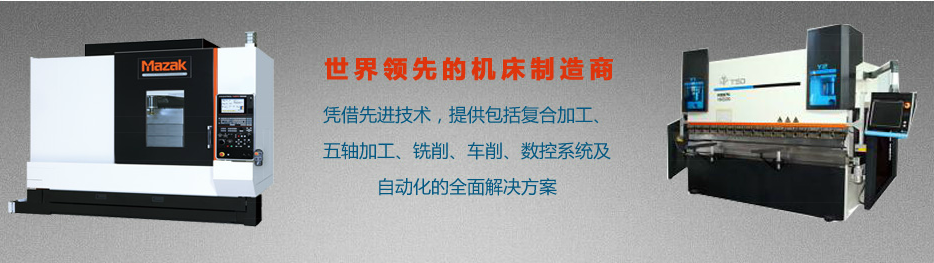
1.高速加工技術的應用優勢及其對機床主軸的要求
1.1高速加工技術的優勢
高速加工技術采用精良的制造設備和材料刀具,可以加快切削毛坯余量的速度,加工出高質量、高精度的復雜零件,同時還可以降低加工成本,提高加工效率。高速加工的應用優勢主要體現在以下幾個方面:大幅度縮短加工時間,1臺高速機床可替代4臺普通數控機床;發熱小,切削速度快,零件變形小,可對薄壁零件進行加工;表面加工質量高,且加工完畢后無需再用磨削機床加工;加工的零件具有較好重復性,能夠應用于模具制造行業電極加工;機床占地面積小,僅需要少數工人;有利于縮短交貨期,加快投資成本回收。
1.2高速加工技術對機床主軸的要求
在高速加工的過程中,要求機床主軸應具備足夠高的剛度和回轉精度,基于這一前提,機床的電主軸,需要采用內徑較大、精度較高且高速性能良好的軸承,并且還要配備先進的潤滑系統。同時,電主軸除了要具備較高轉速之外,其低速段還應具備較大的輸出轉矩,只有這樣才能夠滿足精加工和低速重切削的要求。此外,數控加工中心要求主軸能夠精度定位,以滿足自動換刀等操作要求,故此,電主軸應當具備精確的切向準停功能,而為了大幅度縮短輔助加工時間,并進一步提高生產效率,要求機床的電主軸應當具備快速啟停功能。為了滿足高速加工技術對機床主軸的要求,應當不斷加大對主軸軸承關鍵技術的研究力度,這也是本文研究的重點。
2.高速加工中的機床主軸軸承關鍵技術
機床主軸軸承的種類比較繁多,常見的有滾動軸承、磁懸浮軸承、空氣軸承、動靜壓軸承等等。其中滾動軸承具有結構簡單、高速性能良好、成本低廉、剛度大、便于維護等特點,從而使其成為高速加工的機床主軸軸承首選。滾動軸承的關鍵技術主要包括以下內容:結構優化技術、材料技術以及潤滑技術等。下面本文就這三個方面展開詳細論述。
2.1主軸軸承結構優化技術
對機床主軸軸承進行結構優化的首要目的是提高軸承的高速性能,在具體優化設計的過程中,目標函數的確定是關鍵環節,主要包括球的滾動比、接觸應力、剛度、額定動荷載等等,可供優化的變化有球徑、溝曲率系數、球數等。在優先排序的基礎上,對內外套圈和保持架的結構進行優化設計,不但可使軸承的極限轉速大幅提高,而且還能使溫升顯著降低,由此便可以實現軸承的高速性能。對于主軸軸承而言,極限轉速的大小是決定其高速性能的關鍵性因素之一,所謂的極限轉速具體是指軸承在運動的過程中能夠承受最高熱平衡溫度時的轉速極限值。相關研究結果表明,軸承的極限轉速主要與以下因素有關:公差等級、潤滑方式、預載荷、接觸角、軸承的工作狀態以及組配形式等。此外,軸承運行環境中的熱載荷也會對極限轉速有所影響。因軸承轉速受內部摩擦發熱引起的溫升限制,所以當軸承運行過程中的轉速達到某個界限值時,軸承便會由于內部溫升過高出現熱粘著效應,這樣一來,軸承便無法繼續工作。
2.2軸承潤滑技術
油氣潤滑是高速加工機床電主軸較為理想的潤滑技術,該技術可根據實際潤滑的需要,在不經過霧化處理的情況下,直接將少量潤滑油用壓縮空氣不斷地輸送到需要潤滑的部位。油氣潤滑技術在輸送潤滑油時具備實時、定量、均勻的優勢,這種供油方式能夠確保需潤滑的部位始終不缺潤滑油,并且有效防止因潤滑油量過大而產生較大阻力,避免溫度上升。油氣在潤滑的過程中處于相互分離的狀態,壓縮空氣不僅能夠為油氣輸送提供動能,還能夠對軸承進行冷卻,清除軸承內部雜質。與油霧潤滑相比,在相同工況、轉速的主軸軸承條件下,油氣潤滑能夠降低軸承外圈溫度9-16℃,提高軸承速度因素25%以上。為保證油氣潤滑裝置正常工作,一般情況下油氣潤滑裝置由專業的電主軸公司制造,并且規定潤滑油達到IS04406的13/10級清潔度標準。
2.3軸承材料技術
鋼制主軸軸承材料既要降低鋼中氧含量和夾雜物的數量,滿足長壽命和超高潔凈的要求,又要改進原有鋼種的化學成分,使其滿足不同使用場合對軸承高性能的要求。近年來,隨著軸承鋼冶煉技術的發展,真空脫氣GCrl5和GCrl5SiMo等材料已經成為高速加工機床主軸軸承的主要材料。同時,由氮化硅陶瓷做滾動體的混合陶瓷球軸承也正廣泛應用于高速機床領域。與軸承鋼相比,陶瓷材料的密度是其40%,線膨脹系數不足鋼的25%。所以,在混合陶瓷球軸承高速旋轉時,能夠減小離心力和摩擦力矩,緩和球與套圈的熱膨脹差所引起的軸承載荷,進而降低軸承摩擦發熱量、減輕磨損程度、提高旋轉性能。陶瓷材料的縱向彈性模量是軸承鋼的1.5倍,因此陶瓷球軸承的剛性也會明顯大于鋼制軸承。此外,在相同結構的前提下,陶瓷球軸承的極限轉速是鋼制軸承的1.2-1.3倍,如果進一步優化陶瓷球軸承的結構,還能夠給予陶瓷球軸承極限轉速更大的提升空間。
上一篇:機床設計中輕量化技術的應用
下一篇:現代機床造型設計的特征與原則