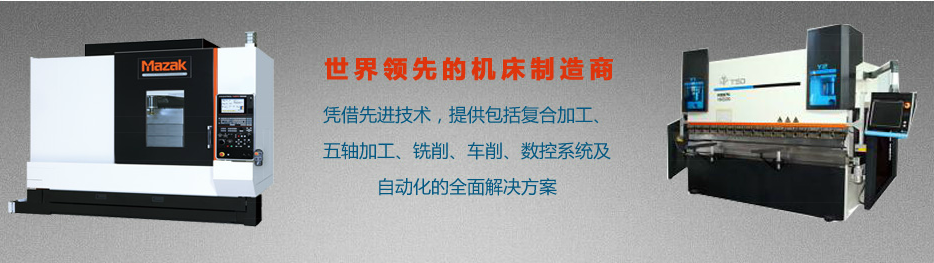
1.機床驅動參數
機床(車床、銑床等)的傳動系統驅動參數由主傳動驅動系統參數和進給傳動系統驅動參數組成。為了達到其相應的加工工藝要求,主傳動或進給傳動系統的驅動電機應具備一定的功率和變速范圍,通常,電機(包括主軸電機和進給電機)的驅動功率稱為動力參數;其轉速及變速范圍,稱為運動參數。
2 動力參數的計算
2.1 主傳動驅動功率的計算
主傳動功率P是選擇主電機及進行機床零件和結構強度計算的主要依據。主傳動功率P可根據切削功率與主傳動效率η 來確定,即:
主傳動的總效率一般可取為η=0.7~0.85,當主傳動鏈較長時,損耗大,傳動效率偏低,可取較小值;當主傳動鏈較短時,損耗小,傳動效率偏高,可取較大值。
式(1)中,切削功率可在選定具有代表性的切削用量(機床設計標準或用戶要求)后,按照下式計算:
式中:—主切削力(N);v—切削速度(m/min);M—切削扭矩(N·m);n—主軸轉速(r/min)。
2.2 進給傳動驅動功率的計算
進給傳動驅動功率包含進給傳動功率和空程快速移動功率兩部分。計算進給功率時,可根據進給力F、進給速度v、機械效率來確定,即:
式中,機械效率取值為0.15~0.2,進給力則根據機床設計時所采用的導軌形式計算得出。
計算空行程快速移動功率時,可根據工作臺或滑板刀架等移動部件的慣性力和傳動摩擦力計算,公式為:
式中:--安全系數,取值1.5~2.5(依安全指標定);M--克服慣性力所需的扭矩(N·m);n—電機轉速(r/min);W—移動部件重力(N);f—移動部件與導軌的摩擦因數,取值0.15~0.2;--快速移動速度(m/min),按照機床設計指標定;η—機械效率,取值為0.15~0.2。
3 運動參數及其范圍
3.1 主傳動極限轉速和變速范圍
主傳動為回轉運動的機床,為了適應切削速度v和工件(刀具)直徑d的變化,主軸的最低轉速和最高轉速可根據下式確定:
式中:--最小加工直徑(mm);—最大加工直徑(mm); --最小切削速度(m/min);—最大切削速度(m/min)。
在主傳動中,最高轉速與最低轉速之比,稱為變速范圍,即:
機床設計時,變速范圍的確定即要考慮工藝需要,也要考慮切削加工的發展趨勢,變速范圍過大,則機床的設計制造成本高;變速范圍過小,則機床通用性不高。
3.2 進給傳動轉速和調速范圍
進給傳動驅動電機的轉速由機床工作臺或刀架的工作進給速度和空行程快速移動速度決定,當電機直接與絲桿相連時,機床工作臺(刀架)由絲桿螺母傳動機構帶動,則電機轉速應滿足:
式中:--工作臺快進速度(mm/min);--絲桿導程(mm)。
如電機與絲桿間有減速機構,則:
式中:i—減速機構傳動比;
如電機通過蝸輪蝸桿減速機構驅動回轉工作臺轉動時,則:
式中:i—電機至回轉工作臺的傳動比;
—回轉工作臺的快進速度(r/min)
由此可見,電機轉速的選擇與機械傳動機構的設計有關。
電機的調速范圍取決于機床加工的最小進給量和快速移動的最大速度。
4總結
機床傳動系統各零部件的形狀、尺寸是根據其動力參數來確定的,而機床的工藝范圍則由運動參數確定,因此,這些參數的理論計算結果為合理的設計機床提供了重要依據。然而,機床的加工范圍廣,加工情況多變,要更準確的選用動力參數及運動參數,除了用理論計算的方法來確定外,還應同時使用類比、測試等方法相互比較來確定。
上一篇:數控機床常見故障分類
下一篇:數控機床維修改造中的常見問題