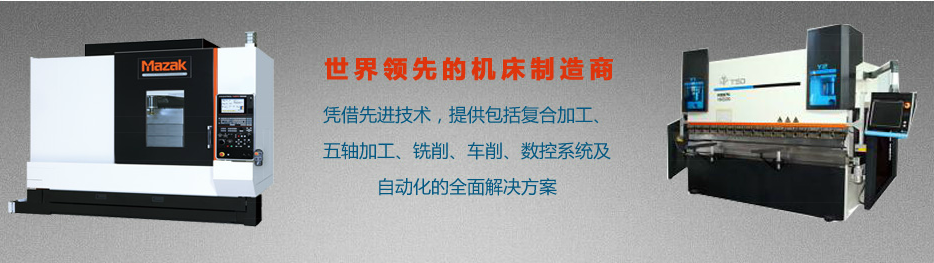
使用數控機床進行車削加工,在選擇數控編程時即應確定切削參數,合理的參數應當能夠最大限度地保障零件加工質量,提高刀具的使用壽命,使數控機床能力得到充分發揮,提升刀具切削性能,且能以較低生產成本獲得較高生產效率。
1.切削參數首先要確定的是主軸轉速
確定合理的主軸轉速才能形成加工所需的恰當切削速度,因此,主軸轉速應當以零件加工所要求的切削速度及棒料直徑為依據來予以確定。從生產實踐中可以發現,除了螺紋加工之外,數控機床車削加工的主軸轉速和普通車削加工大致相同,只需考慮零件加工部位直徑,并依照加工零件及刀具材料等外部條件允許的切削速度進行確定即可。
此外,適當對車床剛性規格差異加以考慮,在數控機床能夠承受的轉速范圍內,盡量選擇接近最大轉速的數值來確定。在數控機床的數控系統控制板上通常會備有主軸轉速的倍率開關,可于加工過程當中按整倍數調整主軸轉速。需要注意的是:在切削過程是干式切削時,應選取相對更小一些的主軸轉速,這個參數一般取有切削液狀態下主軸轉速的70%~80%為宜。
2.切削進給速度參數的合理確定
在單位的時間內,刀具順進給力方向所移動距離即為進給速度,其單位通常為mm/min,也有個別數控機床用每轉進給量(mm/r)來表示進給速度,通常車削進給速度的確定原則如下:首先,在零件加工精度及表面粗糙度等質量要求可以保障的前提下,應盡量選擇高進給速度,以提升生產效率;其次,使用高速鋼刀具車削,或是車削深孔、進行切斷操作時,進給速度應當選擇相對較低的數值;再次,在刀具空行程,尤其是遠距離回零時,應盡量設定更高的進給速度;最后,進給速度這一參數的選擇,必須要與數控機床零件加工時的切削深度及主軸轉速相適應。
3.切削深度參數的合理確定
確定切削深度參數,應當綜合考慮多方向因素的影響。通常應對數控車床、刀具、夾具、零件組成工藝系統剛度、零件表面精度、粗糙度等因素分別進行分析方可確定。在條件允許的情況下,應當盡量選擇相對較大的切削深度參數,以通過減少走刀次數,實現提升加工效率的目的。在零件加工精度及表面粗糙度的要求相對較高時,可考慮留出精加工余量。精加工余量通常較普通車削的余量要小,一般取0.1~0.3mm為宜。
此外,根據實踐生產經驗,通常情況下加工表面的粗糙度值為Ra12.5時,只需一次粗加工即可達到要求。當然,若數控機床的剛度較差、余量過大或是動力不足時,也可分多次完成切削加工過程;在表面粗糙度的要求在Ra1.0~1.6之間時,通??刹捎幂^小切削量來完成精加工。
需要注意的是:吃刀量與數控加工生產率是成正比的,在零件加工工藝及車床、刀具、夾具剛性允許的情況下,應盡量設置更大的吃刀量。在粗加工外,因刀具的加工余量通常不大,一般還需使用精加工工序,吃刀量是指粗加工或半精加工之后留給精加工的余量。余量過多,則刀具易磨損,進而給加工零件的表面質量帶來不利影響;余量過少,則不能消除上粗加工留下的刀路痕跡,對加工零件的表面質量同樣會產生不良影響。
下一篇:淺談提高數控機床加工精度的方法