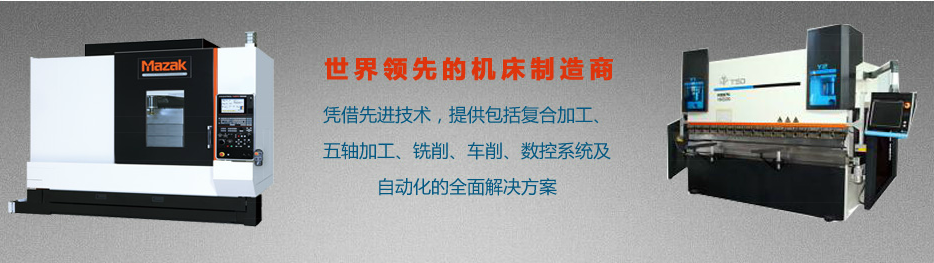
1. 支承件結構設計方法
支承件結構設計方法主要有三種:
經驗類比法、力學方法和數字化設計方法,前兩者為傳統設計方法,后者已逐漸成為當前主流的設計方法。
(1)經驗類比法
經驗類比法是一種改良性質的傳統設計方法,便捷而實用,但需要以大量積累的經驗為基礎。設計人員對已有機床支承件進行小范圍的改進或者根據類似機床支承件結構提出設計方案,設汁全新的支承件。類比法不是簡單的復制和模仿已有的結構設計,作為一種設計方法,它的成功通常離不開力學理論的分析、校核和大量的模型試驗及實物試驗的驗證。類比法要適用于床身等鑄造大件的設計。
(2)力學方法
力學設計方法主要針對機床的整體剛度,利用力學理論(如材料力學、結構力學和彈性力學等)對機床進行剛度設計。通過支承件的合理布局,減小其所受彎矩和扭矩,對支承件進行應力應變的物理性能分析。進而確定支承件材料,整體結構形式,設計參數及筋板的布置形式。通常力學設計方法同樣還需較多的試驗驗證和結構改進。相對于類比法,力學方法已表現出其優越性,走出了模仿的階段,設計自主性得到了提高。力學設計方法主要用于機床支承件焊接結構的設計。
(3)數字化設計方法(有限元法)
數字化設計屬于計算機輔助分析(CAA)和輔助設計(CAD)的范疇。當前,有限元法是最具有代表性和應用范圍最廣的數字化設計方法。在進行機床支承件的結構設計時,有限元法集結構性能分析、結構拓撲優化和尺寸優化于一體,幾乎貫穿了從概念設計到性能驗證的全過程。
類比法和力學方法等傳統設計方法由于在進行分析和判斷時存在大量的主觀經驗、近似和簡化操作,造成準確性不足;由于資金、時間和試驗的限制以及反復“試驗一改進設計一再試驗”的繁瑣過程造成的龐大工作量,而且形成的設計方案往往只是可行方案,而非最優方案。而數字化設計方法借助于計算機工具和有限元軟件,進行支承件結構設計時的幾乎所有工作,如建模、優化、性能分析和對比都在計算機上完成,只需做少量的試驗即獲得支承件的最優設計方案,其優勢是傳統設計方法無法比擬的。
2 支承件結構設計現狀
隨著計算機技術的發展和結構分析與優化軟件的普遍應用,機械結構設計己逐漸趨向于數字化設計。特別是在航空航天、汽車、造船及國防兵器等裝備制造業,以有限元法為代表的數字化結構分析、設計與優化手段已得到廣泛應用。
機床支承件結構設計的目的是以最低的成本獲得性能最佳的支承件結構,最終提升機床整機的綜合性能。由于設計階段決定了整個產品成本和質量的80%左右,其后的改進和優化措施影響有限,所以設計對于產品的重要性不言而喻。而設計的初始階段(概念設計)在很大程度上有決定了設計階段的大部分內容。
在機床概念設計階段,時間限制和信息不確定性等給結構設計帶來了困難。通常,根據機床規格給出的幾何限制和功能要求可以大致確定機床的布局形式、支承件的幾何尺寸和結構形式。
機床概念設計階段的設計過程可分為三個步驟:
(1)整體布局設計,大致選擇機床支承件;
(2)支承件設計,分別對各個支承件進行結構設計,選出性能最佳的支承件結構;
(3)將各個支承件組合形成機床整機概念結構,比較其主要性能指標(主要為剛度)并進行選擇。結構性能分析、結構優化和輕量化設計與機床支承件結構設計密切相關。
以下將對三者的研究現狀進行分析和歸納。
(1)支承件結構性能分析
機床及其支承件的結構性能分析是結構設計和結構優化的必要環節。進行支承件結構設計時,通過性能分析可以判斷設計方案的性能指標是否滿足設計要求;進行支承件結構優化設計時,原方案的性能分析結果,如位移(剛度)、固有頻率,除了可用于優化方案性能對比和檢驗外,還可為優化過程中的優化設置提供參考?,F階段支承件結構分析類型主要有靜態特性分析、動態特性分析和熱特性分析。
機床結構性能分析包括整機性能分析和支承件性能分析。用于整機分析的模型是包括各個支承件和連接結構的裝配體,一般用于考察機床的總體性能。進行機床整機性能分析的目的是更全面地了解其各項性能和狀態,用于性能驗證和檢驗,或者服務于結構優化和改進。
(2)支承件結構優化
傳統的結構優化以結構分析為基礎和主要內容,而且摻雜了較多的主觀因素。其優化過程為:原方案結構分析一發現薄弱環節一改進設計一結構分析。如此反復循環,直到改進方案滿足要求。而現代結構優化指數值結構優化,是最優化技術和有限元法相結合的產物。它借助于計算機及結構優化軟件,以數學規劃為理論基礎,結合力學分析方法,將設汁問題的物理模型轉化為數學模型,運用最優數學理論,在給定的約束條件下找到滿足設計目標的最佳設計方案。其優化過程為:結構分析一搜索(結構設計、分析和優化)一最優設計。其中搜索階段的設計、分析和優化為計算機自動完成,它對某種設計方案進行結構分析和對比,判斷是否達到設計目標,若達到,則該設計方案輸出為最優設計方案;若未達到,則繼續按照某種規則進行設計方案修改和分析對比,直到找到滿足設計目標的最優設計。
?、俳Y構優化數學模型
設計變量、目標函數和約束條件為結構優化設計的三要素。其中設計變量為自變量,它在優化過程屮發生變化導致設計對象結構及其性能的改變;目標函數為從變量,是關于設計變量的函數;約束條件為優化過程必須遵守的前提條件,如某些性能要求。結構優化設計的標準數學模型如下:
最小化(Minimize):
式中, f(X)是目標函數,如結構質量、位移等;gi (X)和hK (X)為約束函數,如靜動態剛度、強度等;X=x1,x2,…,xn是設計變量,Xu和XL為X的上下限,其中上角標U指Upper Limit,L指 Lower Limit。
?、诮Y構優化方法
現階段結構優化方法主要有數學規劃法和準則優化法,它們與非線性規劃法以及線性和非線性相結合的混合法同屬傳統優化設計方法。
?、劢Y構優化類型
結構優化一般分為四種類型或者說由難到易的四個階段,分別為結構類型優化、拓撲優化(包括整體與局部)、形狀優化和尺寸優化。它們分別對應結構設計的四個不同階段,即總體設計、概念設計、構型設計和詳細設計?,F階段結構優化技術正向著兩個方向發展:細化和綜合。一方面,對于某種優化類型,優化過程劃分為更多的階段,以求獲得更精確的優化結果。另一方面,優化類型和階段的劃分變得越來越模糊,正向著多類型和多層次綜合優化的方向發展。
進行機床支承件結構優化時,一般拓撲和形狀優化之間并沒有嚴格區分開,相應的支承件結構設計階段通常也合并為結構構型階段和詳細設計階段。
(3)支承件輕量化設計
輕量化設計體現了綠色、經濟和節能的現代制造技術要求。隨著機床加工技術的發展,機床的高速度、高精度和綠色制造等特點要求機床支承件必須具有較高的剛度和較小的質量。機床支承件的輕量化設計是解決這一問題的重要途徑。輕量化的發展方向主要有兩個:結構輕量化和材料輕量化前者主要通過支承件結構優化設計來實現。近年來基于自然界輕質高效生物結構的仿生結構在支承件輕量化設計中的應用成為一個亮點后者主要通過選用強度高而質量輕的新型材料來實現,如鍋合金、高強度鋼、工程塑料、泡沫金屬、復合材料和點陣材料等。